Trwałość konstrukcji pod moduły fotowoltaiczne w aspekcie oczekiwań inwestorów
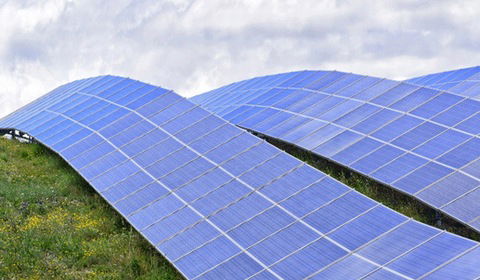
Niniejszy artykuł ma na celu przybliżyć uczestnikom procesu inwestycyjnego budowy instalacji fotowoltaicznych tematykę związaną z wymogami, jakim powinny odpowiadać podkonstrukcje w zakresie trwałości korozyjnej. Zagadnienia te są bardzo często bagatelizowane podczas wykonywania projektów instalacji lub samej realizacji.
Kategorie korozyjne środowiska.
Zgodnie z normą PN-EN ISO 12944-2:2001 rozróżnimy następujące kategorie korozyjności atmosfery i przykłady typowych środowisk:
W treści przywołanej powyżej normy został opisany wpływ środowiska na konstrukcje stalowe, w tym wystawione na działanie atmosfery, jak również te, które są użytkowane jako zanurzone w cieczach. Dodatkowo przedstawiono w niej system klasyfikacji oparty na kategoriach korozyjności różnych środowisk atmosferycznych. Norma opisuje również różne kategorie dotyczące zanurzenia. Na podstawie tych wytycznych każdy uczestnik procesu inwestycyjnego bardzo łatwo może określić, która kategoria korozyjności dotyczy rozpatrywanego przypadku.
Proszę zwrócić uwagę, że na podstawie rocznych ubytku w [mµ] powłoki ochronnej w zależności od kategorii korozyjnej środowiska, w jakim została pobudowana instalacja, można przeliczyć trwałość konstrukcji w relacji do grubości warstwy ochronnej. Oczywiście jest to też uwarunkowane rodzajem powłoki i badań laboratoryjnych z nią związanych. Może się bowiem okazać, że pewne rozwiązania w zakresie ochrony korozyjnej z użyciem profili stalowych lub bez ich użycia, jak to ma miejsce w przypadku profili aluminiowych, posiadają pozytywne raporty z badań lub opinię akredytowanych laboratoriów, które dedykują je do poszczególnych klas agresywności środowiska.
W takich przypadkach każdorazowo producent podkonstrukcji powinien okazać się takimi dokumentami. Tego typu badania są długotrwałe, wykonywane w komorach solnych lub poprzez ekspozycję w danym środowisku, co zajmuje jeszcze więcej czasu.
Fot. Widok stałej stacji korozyjnej użytkowanej przez IMP w Katowicach w warunkach narażenia w atmosferze przemysłowej.
W tym zakresie należy weryfikować wszystkie dokumenty producentów podkonstrukcji, którzy niejednokrotnie próbują dowodzić, że wprowadzili innowacyjne powłoki lub dodatkowe ich zabezpieczenia poprzez malowanie np. wbijanych nóg w celu spełniania wymogów związanych z ochrona korozyjną. Niestety nie mają na powyższe odpowiednich raportów gdyż tego typu badania jak zostało wspomniane wcześniej są po pierwsze czasochłonne oraz muszą być wykonywane przez jednostki naukowe posiadające do tego odpowiedni sprzęt oraz kadrę naukową.
Fot. Próbka z powłoką cynkową Z275 przed ekspozycją w komorze solnej, 384 h (z lewej) oraz ta sama próbka po ekspozycji z dużymi ogniskami korozji (z prawej)
Fot. Próbki z powłoką cynkową wzbogaconą aluminium i magnezem przed ekspozycją w komorze solnej, 384 h (z lewej) oraz po ekspozycji w komorze solnej – brak korozji (z prawej).
Standardowe rozwiązania powłok antykorozyjnych posiadają potwierdzenie, że zostały poddane badaniom i zaszeregowano je w zależności od kategorii korozyjnej środowiska. Dotyczy to miedzy innymi konstrukcji stalowych z powłoką Z275 wg PN-EN 10346, którą nanosi się na blachy i taśmy o grubości do 2,5 mm. Naniesienie powłoki cynkowej następuje w hucie przez zanurzenie blachy w kąpieli z roztopionego metalu zawierającej co najmniej 99 proc. cynku. Większość wyrobów jest w ten sposób pokrywanych powłoką o typowej grubości 20μm (od 15μm do 27μm).
Zgodnie z obowiązującymi wytycznymi i normatywami, blachy z tego typu zabezpieczeniem antykorozyjnym nie nadają się do stosowania na zewnątrz. Są dedykowane tylko do pomieszczeń o kategorii korozyjności C2 – budynków nieogrzewanych, w których może mieć miejsce kondensacja pary wodnej, np. magazyny, hale sportowe. Niestety w praktyce zrealizowano już wiele instalacji fotowoltaicznych z wykorzystaniem elementów pokrytych powłoką Z275, zlokalizowanych w miejscach, których agresywność środowiska sklasyfikowano na poziomie C3 i C4. .
Podobnie sytuacja wygląda w przypadku wyrobów stalowych zabezpieczanych cynkowaniem zanurzeniowym według PN-EN ISO 1461. Wyroby z powłoką cynkową nanoszoną metodą zanurzeniową nadają się do środowisk z kategorią korozyjności C3 oraz z pewnymi ograniczeniami C4 (np. zakłady spożywcze, pralnie, browary, mleczarnie). W pomieszczeniach o kategorii korozyjności C4 i C5 powinny być stosowane wyroby ocynkowane, a następnie pomalowane farbami epoksydowymi.
Należy podkreślić, że przedmiotowe normy i przepisy nie odnoszą się do elementów wbijanych w grunt, a jedynie elementów napowietrznych. W przypadku konstrukcji osadzonej w gruncie producenci powłok lub systemodawcy konstrukcji powinni się legitymować badaniami, które dowodzą możliwości ich stosowania w tym zakresie. Oczywiście każde modyfikacje, związane choćby z dodatkowym malowaniem bez przeprowadzenia badań sprawdzających, nie gwarantują spełnienia tych wymogów.
Zjawiska korozji między materiałowej (stykowej)
Instalacje fotowoltaiczne w zależności od miejsca wbudowania, rodzaju konstrukcji i sposobu montażu są wykonywane z różnych materiałów. Należy wówczas przestrzegań kilku najważniejszych zasad. Głównie w instalacjach dachowych ale też naziemnych stosuje się elementy profili aluminiowych skręcanych ze sobą w sposób mechaniczny i niejednokrotnie obudowane blachami. W tym zakresie zakazane jest używanie jakichkolwiek elementów wykonanych ze stali czarnej ocynkowanej, które bezpośrednio stykają się z aluminium. W przypadku blach należy odizolować dwie powierzchnie (stal ocynkowana i aluminium) przekładkami z folii lub taśm. Natomiast w przypadku wkrętów i śrub do aluminium można stosować tylko wykonane ze stali nierdzewnej o klasie A2 lub A4. W przeciwnym razie już po kilku miesiącach zauważymy powstające ognisko korozji w miejscu zastosowania np. wkrętu ocynkowanego.
Często spotyka się również z zastosowanie kotew ocynkowanych mocujących instalację do budynku poprzez aluminiowe marki/konsole. W takim przypadku zachodzą dwie niezgodności. Pierwsza to korazja między materiałowa na styku kotwy z konsolą/marką montażową. Druga zaś dotyczy stosowania kotew w odmianie ocynkowanej na zewnątrz budynku. Otóż, ze względu na warstwę ochrony korozyjnej (ocynk), tego typu elementy są przeznaczone do stosowania tylko i wyłącznie wewnątrz budynków w pomieszczeniach suchych. Biorąc pod uwagę powyższe mocowania wraz z wkrętami używane w kontakcie z aluminium powinny być zawsze wykonywane łącznikami nierdzewnymi. Aluminium w stosunku do stali nierdzewnej jest anodą, a stal nierdzewna katodą. W związku z powyższym połączenie aluminium i stali nierdzewnej teoretycznie mogłoby powodować powstawanie różnicy potencjałów, co w konsekwencji może być przyczyną występowania zmian korozyjnych.
Należy jednak pamiętać, że odstępstwem od tej reguły są przypadki połączeń metali o znacznej różnicy potencjałów, gdzie ważnym czynnikiem jest stosunek powierzchni anody do katody. Duża powierzchnia katody (stali nierdzewnej) w stosunku do małej powierzchni anody (aluminium) przyspiesza proces korozji natomiast odwrotny przypadek w skuteczny sposób to eliminuje. Specyficzna budowa podkonstrukcji pod moduły fotowoltaiczne charakteryzuje się dużą powierzchniową profili aluminiowych w stosunku do występujących punktowo łączników nierdzewnych. W tych konkretnych rozwiązaniach różnica wielkości potencjału stopu aluminium w stosunku do stali nierdzewnej jest dużo mniejsza, a tym samym nie zachodzi zagrożenie korozyjne.
Dodatkowo należy nadmienić, że łączniki nierdzewne w konstrukcjach aluminiowych nie rdzewieją ponieważ podatność metali i stopów na korozję elektrochemiczną jest zależna od składu chemicznego i struktury fazowej stopu. Odpowiedni dobór składu chemicznego powoduje przesunięcie standardowego potencjału elektrodowego do wartości dodatnich, zapewniając wysoką odporność na korozję. Działanie takie w przypadku stali nierdzewnych zapewnia dodatek ok. 18 proc. chromu.
Dodatki innych składników stopowych, takich jak mangan, nikiel, miedź, powodują uodpornienie się stali na bardziej agresywne działanie środowiska korozyjnego (np. kwasów, zasad). Czyli to dodatek chromu pozwalający na wytworzenie warstwy pasywnej zapewnia dostateczną ochronę przed korozją. To właśnie warstwy pasywne są odpowiedzialne za brak reakcji stali nierdzewnej i aluminium, gdyż posiadają zbliżony potencjał elektryczny. Kontakt tych warstw przy połączeniu nie wywołuje zjawiska korozji elektrochemicznej.
Uszkodzone podczas montażu warstwy pasywne w krótkim czasie ulegają regeneracji, zapewniając odpowiednie własności ochronne. Warstwa pasywna zapobiega też korozji w przypadku kontaktu stali nierdzewnej z alkalicznymi materiałami budowlanymi takimi jak beton, zaprawy itp. czego z kolei nie można stwierdzić w przypadku elementów wykonanych z aluminium. W takich przypadkach należy zawsze stosować przekładki odizolowujące obydwa materiały, w tym przypadku beton i aluminiowa konsola.
Cezary Rutkowski, Cr-consulting
artykuł sponsorowany